Common faults with heat pumps: Causes, solutions & when a specialist is needed
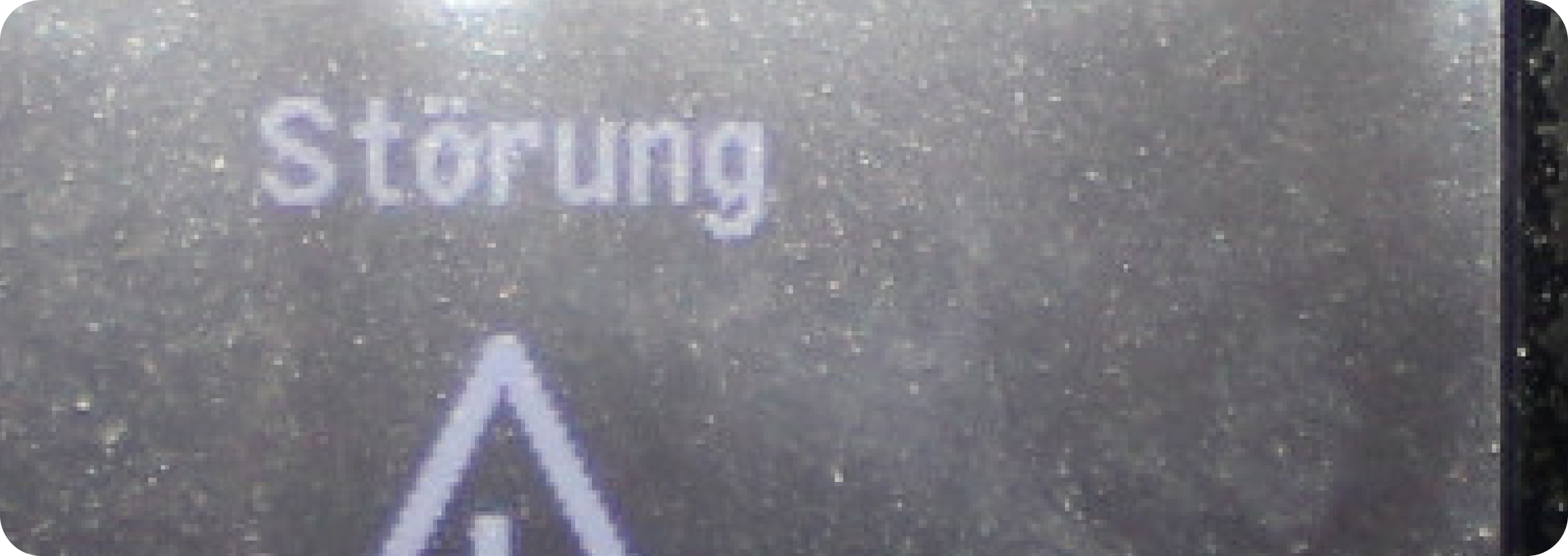
Heat pumps occasionally malfunction during operation. Small errors often lead to noticeable restrictions. Sometimes a look at the settings is enough, in other cases only a specialist company can help. In this article, you'll learn which problems are most common and how you can fix them.
Common faults with heat pumps
The most common malfunctions with heat pumps include temperature problems, icing of the outdoor unit, unusual noises, frequent clocking and error codes on the display. The causes range from harmless settings to technical defects. The following table provides an initial overview:
Heat pump does not heat
If your heat pump no longer heats, this is usually due to incorrect settings or a faulty temperature sensor. In many cases, the heating curve Set too low or the heating mode was inadvertently deactivated. As a result, your home stays cold even when the system is running. First check the heating curve in the controller and activate the heating mode. If the heat pump still remains inactive, you should hire a specialist company. There could be a technical problem with the sensor or the controller.
Iced outdoor unit
One Icing of the outdoor unit occurs when the defrosting system is not working correctly or the location has been selected unfavorably. The heat pump draws moisture from the air. Ice forms at temperatures around zero degrees. If the automatic defrost system fails, the ice persists. The result is poor heating capacity or a complete failure. Switch off the heat pump and let the ice melt. Check whether the defrost program is active. In the event of repeated icing, a specialist company should check the system.
Unusual noises
If your heat pump makes unusual noises, the cause is usually mechanical components or air in the system. Hum, knock, or whistle may indicate a loose fan, air bubbles, or compressor damage. Such noises often occur when starting or defrosting. Have the system checked immediately if the noise persists. In this way, you can avoid subsequent damage and ensure the life of your heat pump.
Heat pump does not start
If your heat pump does not start, there is often a power problem or an internal fault. First, check whether fuses have been triggered or if there is a power failure. Interfered communication with the thermostat can also prevent starting. If the display is completely off, it is likely that there is an electrical problem. If the display is lit, it often helps to look at the error display. Write down the error code and contact a qualified workshop if you are unsure.
Error code on the display
An error code on the display means that the heat pump control system has detected a fault. Common codes relate to water pressure, sensors, or the refrigerant circuit. Such failures often result in limited operation or a complete shutdown. Look for the error code in the user manual. You will usually also find recommendations for action there. Some errors are easy to fix. For more complex reports, a specialist company is required.
Heat pump cycles frequently
If your heat pump cycles frequently, i.e. switches on and off constantly, this is a sign of a incorrect interpretation or control. This often happens with oversized systems or when there is no buffer tank. The system reaches the target temperature too quickly and shuts off immediately. This behavior increases wear and results in higher power consumption. Check the heating curve and adjust the operating times. In the long term, a hydraulic balancing or retrofitting a suitable storage system.
Hot water is too cold
If the hot water no longer reaches the desired temperature, this is usually due to the target temperature or the hot water tank. A faulty sensor can also cause the problem. As a result, your hot water is only heated lukewarm or not heated at all. Check the setting in the hot water menu of your controller. If everything is correct there, a specialist company can test the sensors and the memory.
Power consumption is too high
Excessive power consumption with your heat pump is often caused by incorrect settings or an inefficient mode of operation. A lack of hydraulic balance or poor insulation can also be the cause. You usually notice this in rising electricity costs. Check the heating curve and activate night reduction.
Pressure is too low
Too low pressure in the heating circuit is caused by water losses or air in the system. The water pressure drops below the target level and the heat pump shuts off. You can see this on your system's pressure gauge. Refill heating water until the pressure is back to normal. If the pressure drops again, you should hire a specialist company to detect leaks.
Heating capacity is not enough
If the heat output of your heat pump is too low, this is often due to clogged filters, silted hydraulics or incorrect settings. The rooms remain too cool despite the system running. Adjust the heating curve and clean the filters. Hydraulic balancing can significantly improve performance. In older systems, sludge removal from the heating circuit often helps.
What can users do themselves?
Some problems with heat pumps can be resolved without specialist knowledge. The prerequisite is that you have the operating instructions at hand and that you are familiar with how to control your system. You can usually solve the following problems yourself:
- Wrong heating curve or operating mode: If the heat pump does not heat properly, this is often due to a heating curve that is too low or the wrong mode. Open the settings in the control unit and check whether the heating mode is activated. If necessary, increase the flow temperature in small steps.
- Iced outdoor unit: Slight icing can be repaired by briefly switching off the heat pump. Then activate the defrost program. Make sure that air exchange around the outdoor unit is not blocked.
- Check power supply: If the heat pump does not start, check the fuses and the FI switch. Switch the device off and on again. A simple restart fixes many control errors.
- Error message on the display: Read the error code on the display and look it up in the user manual. These are often harmless warnings that disappear when you change the settings.
- Too low water pressure: If the water pressure in the heating system drops, you can add heating water via the refill valve. Pay attention to the recommended pressure value in the instructions.
- Clogged air filter: Contamination can reduce efficiency in air-to-water heat pumps with air filters. Remove the filter carefully, clean it with water and reinsert it.
- Check night reductions or time programs: If the heat pump does not heat continuously, time programs are often active. Check the timer functions and adjust them to your daily rhythm.
- Detect slight noises: Humming or flowing noises are often harmless. Check whether pipes are against walls or whether there is air in the radiators. A simple venting can help.
When should users call a specialist company?
A specialist company should always be called when the cause is unclear or there is a technical defect. Professional help is also required for safety-related problems or interventions in the refrigeration circuit. A specialist company is required in the following cases:
- Heat pump does not start despite the power supply: If the system does not respond despite a correct power supply, there is probably a fault in the controller or in the compressor. You can't fix that yourself.
- Error codes with technical reasons: Fault codes that indicate sensor failure, refrigerant pressure, or compressor failure require diagnostic equipment and expertise. Only a specialist company can reliably identify and remedy the cause.
- Refrigerant loss or leaks: As soon as there is a suspicion of a leak in the refrigeration circuit, a certified refrigeration technician must be called. The handling of refrigerants is regulated by law and must not be handled by yourself.
- Icing despite defrosting program: If the outdoor unit freezes over and over again and the defrosting system does not work, there is a deeper fault. The controller, sensors, or valves could be faulty.
- Strong or persistent noises: Popping or grinding noises indicate damaged components such as bearings, fans or the compressor. This damage may worsen and cause follow-up costs.
- Frequent cycle of the heat pump: Continuous switching on and off puts a strain on the system. This is usually due to an incorrect design or faulty hydraulics. The specialist company can provide targeted remedies with an efficiency analysis.
- Too low heating output despite correct settings: If, despite a correctly adjusted heating curve, sufficient heat is not provided, the cause is often found in silted heating circuits, defective heat exchangers or internal control problems.
- Pressure drop despite refilling: If the water pressure drops again and again, there is usually a leak in the system. The specialist company can locate and repair the leak and refill the system.
- Hot water is no longer heated at all: If the water heating system is no longer working, there may be a defect in the tank, sensor or diverter valve. These components may only be opened and repaired by trained personnel.
How do I find a good specialist company?
Ideally, the same company that installed your heat pump should also be responsible for maintenance and repair. The original installer knows the system, has the documents available and can react quickly in the event of faults.
If that is not possible, pay attention to experience, specialization and transparent offers when looking for a new specialist company. Good companies specialize in heat pumps, regularly take part in training courses and are active in the HVAC trade (sanitation, heating, air conditioning).
A reliable specialist company comes to an on-site visit, checks the layout and discusses technical details with you. He prepares a written offer with clear information on services, costs and time frame.
Certificates from manufacturers such as Vaillant, Stiebel Eltron or Viessmann indicate that the company is familiar with the appropriate devices. Membership in a guild or professional associations is also a good sign.
How to avoid disruptions
Many problems with heat pumps can be avoided if you adjust your system correctly and check it regularly. You can prevent failures and extend the service life by taking the following measures:
- Annual maintenance by a specialist company: An annual inspection ensures that sensors, pressure, filters and control are working properly. In this way, potential defects can be identified and repaired early before major damage occurs.
- Regular monitoring of settings: Check the heating curve, operating mode, and time programs. Incorrectly set values often result in insufficient heating capacity or unnecessarily high power consumption.
- Watch for error messages: You shouldn't ignore error codes on the display. Read the meaning in the user manual and act quickly. Early intervention prevents subsequent damage.
- Take noises seriously: Noises such as knocking, buzzing, or whistling may indicate mechanical problems. If they are identified early, they can usually be resolved without major effort.
- Keep outdoor unit clean: Remove leaves, snow, and other contaminants around the outdoor unit regularly. This ensures the air supply and prevents icing.
- Check heating pressure regularly: Too low water pressure can impair heating output or cause the system to shut down. Pay attention to the pressure gauge value and refill heating water if necessary.
- Perform hydraulic adjustment: Hydraulic balancing ensures that all radiators are evenly supplied. As a result, the heat pump works more efficiently and cycles less.
autarc: Your partner for efficient planning of heat pumps — find out more now!
Rely on quality and expertise when planning and installing heat pump systems. With our Heat pump check receive comprehensive support so that you can implement your projects efficiently and sustainably. Contact us today and benefit from our expert knowledge!